The Melbourne factory already produces more than 40 cast aluminium-alloy components for a number of Nissan vehicles – including the all-electric Leaf hatchback – and the Japanese car-maker’s premium Infiniti brand, but the six new parts will be destined for new “EV-style” vehicles that have not yet been confirmed.
Nissan Casting Australia Plant (NCAP) describes itself as an “electric vehicle part specialist” and is most proud of the almost impossibly complex Leaf drivetrain water jacket.
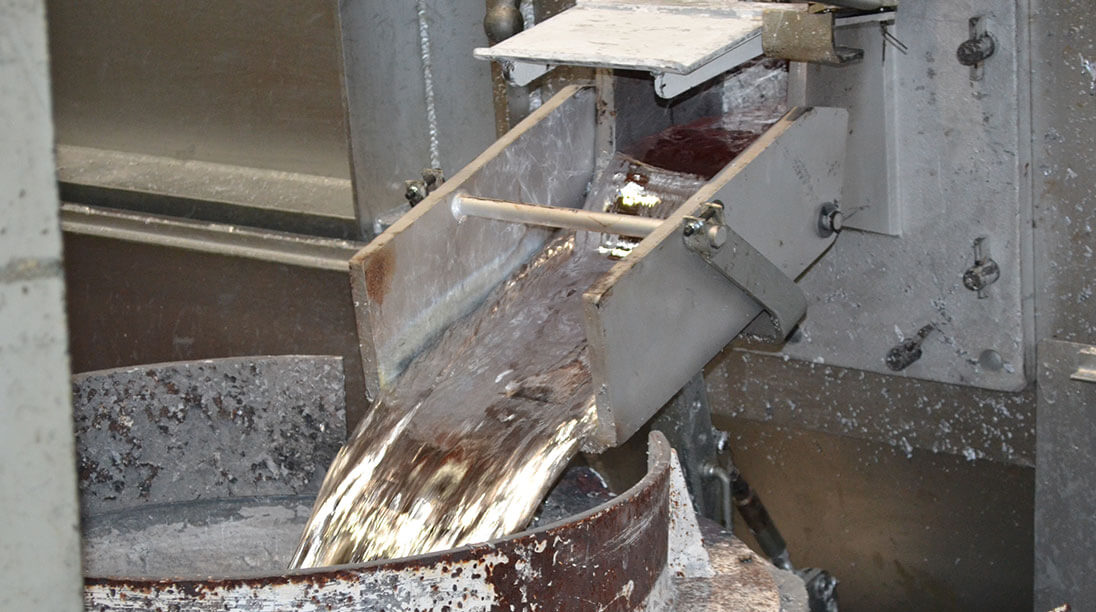
River of silver: A deal to produce new cast aluminium EV parts has secured the future of Australia’s Nissan die-casting plant for the coming years.
However, the set of new parts will mark the next chapter in its electrification story.
Speaking exclusively to GoAuto at an in-depth tour of the Dandenong South facility, NCAP managing director Peter Jones presented the new components and explained the importance of the contract.
“These are the new parts that we’ve won over the last 12 months,” he said. “These are in production now but the cars aren’t yet. They are new EV-style parts. It’s about 40,000 parts a month.
“Prior to April 2016 we had a bit of a lull and we were well below our limit of 10,000 tons but over the last year we picked up a whole heap of new parts. That’s put us right up. We’re not above capacity but we are heading towards it.
“We have contracts that run through to 2019 and we still have parts that will go past 2020.”
All staff at the facility were on strict instructions to remain tight-lipped about the future models during our visit, but the six intricate pieces are tangible evidence of both the new electrified models and the Australian company’s relevance in global development.
With more than one model destined to receive the parts, a Leaf replacement and other models from the Renault-Nissan Alliance are anticipated, and while the company’s products have so far only extended to full EVs, GoAuto believes one of the new models will be a hybrid.
Following the Parisian government’s crackdown on metropolitan emissions, it is likely that Renault has its own zero-emissions model in the pipeline, and sharing vital componentry with its Nissan siblings would be a logical move.
NCAP Gallery – Click to enlarge
It is not known when the mystery models will be confirmed, but our tour of the recently upgraded casting facility revealed production to be well beyond jobbing, development and prototyping stages, indicating production of the complete cars will start soon.
Mr Jones was not willing to identify any of the components but the most abundant appears to be a new cooled casing for a hybrid or electric power management module, not unlike the existing Leaf water jacket, while another significant part appears to be a final drive motor housing.
Winning the contract to manufacture challenging parts has secured the future of NCAP in Australia and Mr Jones said the most recent agreement would safeguard the company’s future.
“We are a specialist in electric vehicle parts and they, by definition, are very difficult. One of the reasons we exist is because we build complex parts,” he said. “We are always looking to the future of EVs and it’s a central part of Nissan’s platform.”
Mr Jones added that the facility’s efficiency and ability to turn projects around rapidly was instrumental in netting the contract.
“The important thing is that it went from concept to reality in less than eight months. It normally takes a lot longer than that,” he said. “Originally these parts weren’t going to come to us, they were going somewhere else and that didn’t happen. We were given a very quick brief to get these things done; we said we could do it, and we delivered.”
In addition to creating revenue for NCAP over the coming years, the successful execution of the EV parts project has showcased the company’s versatility and flexibility and Mr Jones said it would be a simpler process to secure future contracts for difficult parts.
“Because we have delivered this project in under eight months, we’ve demonstrated not only our capacity but our capability,” he said.
“So now, when people from Japan look for a plant that can manufacture these highly complex parts and do it in a time period that wouldn’t normally have been foreseen, they look to us … That makes getting the next one a whole lot easier.”
In a show of confidence for the new line of components, NCAP invested $12 million to enable production.
By Daniel Gardner