In a groundswell being created by the nation’s motor trades bodies, employers are being told they should be thinking about training the next generation of motor business owners rather than training someone to simply swing spanners in the workshop.
The Motor Trade Association of Western Australia CEO Stephen Moir told GoAutoNews Premium: “I tell apprentices that they are not training to be a mechanic, they are being trained as a business owner.
“That’s where they have to set their sights. If you just want to be a tradesperson then that’s great but really, you should set your sights as owning your own business and you can do very, very well.”
Asked if businesses expected government support to take on apprentices, Mr Moir said: “I think this is bigger than a subsidy.
“It’s about actually investing in their business. I think the old days when you trained an apprentice and they didn’t stay with the employer could be changing as well – we are seeing more people stay with the employer.”
Data from the National Centre for Vocational Education Research (NCVER) shows that the decade-long downward spiral of apprentice employment is being reversed.
It shows more automotive businesses are embracing training and the 6000-plus shortfall of automobile-related tradespeople is being turned around.
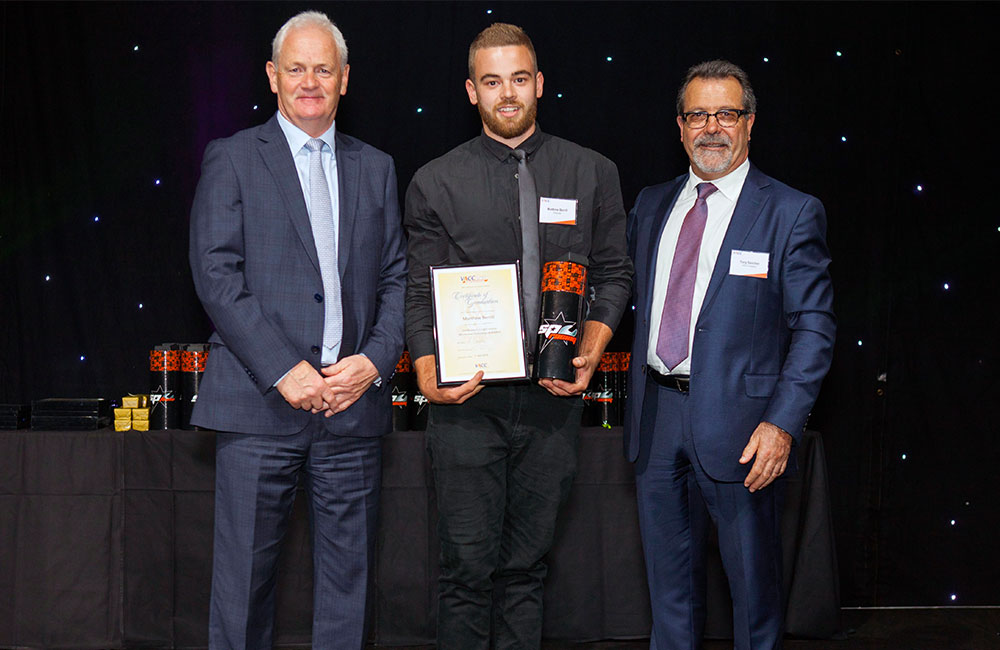
From left: VACC Executive Director Geoff Gwilym, graduating apprentice Matthew Berrill, VACC President Tony Sanchez
In the December quarter of 2017, the NCVER reported an intake of 35,945 trade and non-trade apprentices and trainees, up 7.6 per cent on the same period in 2016. There are now 256,140 people in training or apprenticeships in Australia.
NCVER said that the number of apprentices entering the automotive industry was up 20.9 per cent in the December quarter, representing the biggest increase across all trades.
But the numbers vary across the country. In Victoria, the Victorian Automotive Chamber of Commerce (VACC) said apprentices in the automotive sector had dropped by “a couple of thousand over the past few years”.
VACC head of marketing, media, communications and publications, David Dowsey, said there had been upwards spikes in some sectors “but nothing to fill the ever-growing skill shortage in the automotive industry”.
But in WA, the Motor Trade Association of WA told that it is seeing an increase in businesses taking apprentices.
“It is turning the corner,” said Mr Moir.
“There was concern there for a while but now we are seeing companies engaging. Even the small independents, with one or two staff, are now bringing apprentices in because they realise they have to invest and now is a good time to do this.
“We are bucking the trend and the skill shortage in WA is easing,” Mr Moir said.
“The figure is about 6000 of positions open now in the automotive industry in Australia. We have the biggest labour shortages in the automotive industry in panel and paint and in heavy trucks.
“So (Caterpillar distributor and heavy vehicle retailer and repairer) Westrac has re-engaged in training and has a college near the Perth airport and are running schools and that’s great because there is a shortage in that area.”
Mr Moir said that in WA the skill shortage in automotive was 1558 positions and of that, the light vehicle mechanic shortage is 660.
In the bigger picture, there are about 27,000 positions open in the automotive industry – including about 6000 trade vacancies – from service advisors to dealer principals, according to Australian Bureau of Statistics data from December 2017.
The difficulty in obtaining apprentices in areas such as panel and paint has led to one trainer, Vantage Automotive, opening its own body repair facility.
Vantage Automotive is a major provider of government-funded vocational learning and development services to automotive manufacturers.
It said that the focus of the body repair facility was to deliver manufacturer training to its clients.
“However, due to the high quality of the facility, highest delivery standards, and the ability to support increasing industry requirements, Vantage Automotive has now broadened their reach to encompass a global body repair training footprint,” the company said.
“The facility now delivers body repair training to New Zealand and Asia-Pacific markets.”
The company operates the Jaguar Land Rover global body repair pathway to the Asia-Pacific market and employs a specialised trainer to develop and deliver the program in steel and aluminium welding, bonding and riveting, smart repair and composite materials.
Vantage Automotive is now looking to establish new partnerships with automotive clients to provide branded body repair training programs.
“The training workshop has been specifically designed and equipped with the latest technology to deliver the very best in aluminium and steel welding, bonding and riveting, and paintless dent repair.”
The VACC’s David Dowsey said: “The future of the automotive industry depends heavily on our ability to train and place the next-generation workforce.
“VACC Auto Apprenticeships is the largest automotive apprentice employer in Victoria and recently graduated 121 apprentices at a ceremony in Melbourne, attended by more than 400 people.
“Breaking this down, we had 40 school-based graduates, 69 apprentice graduates, and 12 diploma graduates.”
Skill shortages are severe in the auto industry, and it is predicted that they will get worse.
According to Directions in Australia’s Automotive Industry, written by VACC’s Research Unit, almost half of all Australian automotive businesses are impacted by skill shortages, which is holding back investment and growth in the industry.
One example of making the transition from apprentice to business owner is David Dye, owner of BMW and prestige-car retailer and technical centre 3MW in Perth’s near-northern CBD suburb of Osborne Park. (see Breakout)
His story is matched by individual companies reporting growing apprentice numbers, including Toyota Material Handling Australia (TMHA) that inducted a record 13 apprentice forklift technicians in its annual intake.
It received 878 applications for apprenticeships from around the country, a 75 per cent increase on the 2017 figure.
TMHA national technical advisor and trainer Gerry Larney said 13 apprentices was a record annual intake and continues Toyota’s commitment to industry-leading skills training.
“We currently have 50 apprentices completing their four-year courses across our 17 branches and a total of 450 staff in product support roles,” he said.
“TMHA views the apprentice program as a cornerstone in providing the highest levels of product support,” he said.
“It is a real investment in our future, as today’s apprentices are tomorrow’s technicians.”
Employers and prospective apprentices can contact agencies such as BUSY At Work, an Australian Apprenticeship Network Provider that offers free recruitment services for employers and career advice to job seekers.
BUSY delivers the Australian Apprenticeship Support Network (AASN) in Queensland and in Western Australia under the “apprenticeship community” brand.
BUSY has over 40 offices throughout Queensland, WA, Victoria and New South Wales.
By Neil Dowling